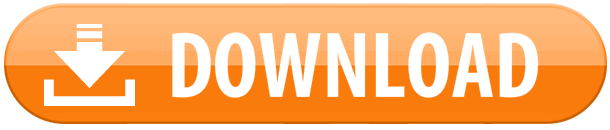
MACH3 software parameter settings Mach3 software ready This card is a Mach3 USB interface 4/6-axis motion control card. The latest version of Mach3 official website. 3.2:Mach3 could not find the usb the motion card and prompt “Is the Xpod Inserted ok?it has ceased to respond”. Mach3 Addons are a solution for using Mach3’s wizard capability to simplify the creation of G-Code files. This package will minimize the time it takes to go from “start to part” by minimizing the need for using a G-code editor. This package is great for simple, unchained operations, that will only be run one time.
Introduction
Included with the CD/USB stick that came with your MX3 is a copy of the trial version of Mach 3. Should you be unable to find your CD, you can download the full contents here.
Installation
The file name you are looking for is Mach3VersionR3.041. You'll want to follow the usual process for installation, but please note that for 64-bit computers that you will need deselect LoadMach3Driver as it would cause installation errors.
Mach3 License
As mentioned, the mach3 software we provide is a trial version. It can only run up to 500 lines of G code, and does not enable the testing of machine functions. If you like it and want the full version, you can purchase it from us here or through the mach3 official website.
Mach3 Usb Cnc Controller Software
Mach3 Configuration & Plug-In Import
Copy the file Mach3Mill.xml and Plugins folder from CD, and use it to replace the file of the same name in the mach3 installation directory, as shown in the following figure:
Starting Mach3
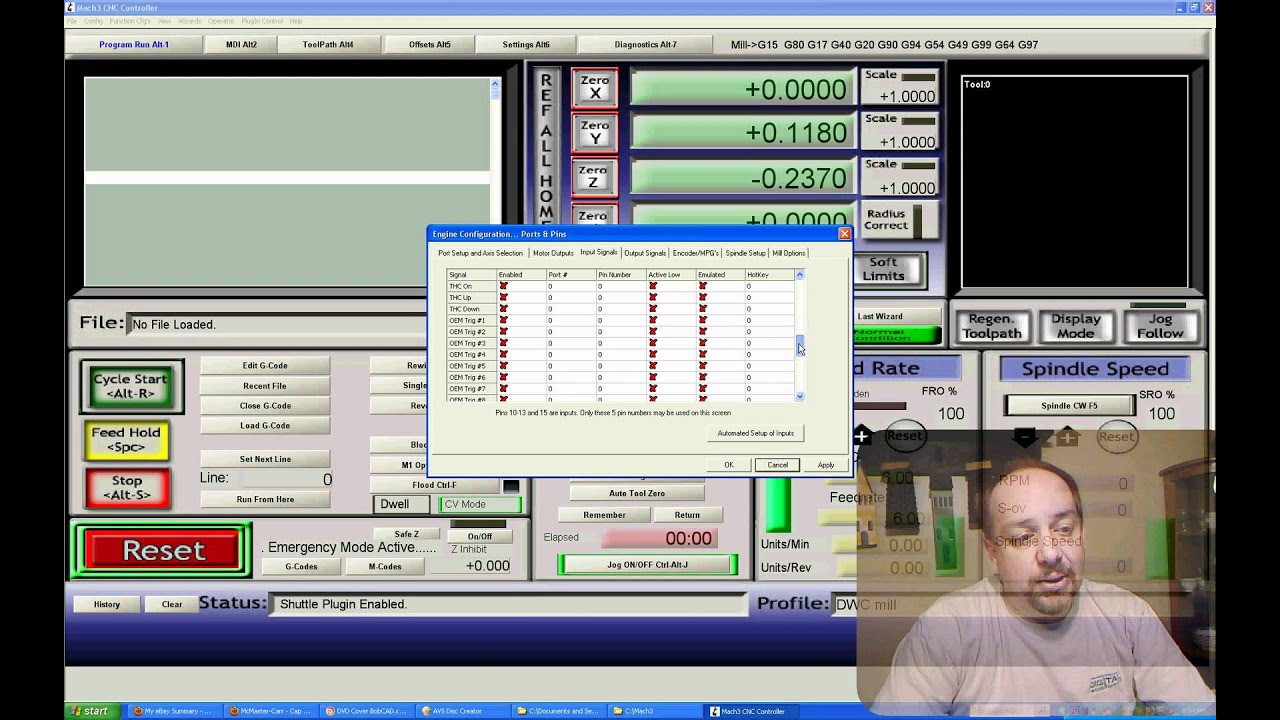

To launch the software, click the desktop icon that says Mach3Mill. When you do so a text box will pop up that asks you to select from a number of devices connected to your computer. select the BL-UsbMach-V3.2, you can also select “Don't ask me this again”.
Engraving Process Example:
Mach 3 Cnc On Disk
- Reset the software and make sure that the bottom status bar says 'Usbmach connected' as shown here:
- Click 'Load G-Code' to import the engraving code, for example, import the NC file in the CD: sainsmart.nc, as shown below:
- Use the manual function to move the X Y Z axis to find the machining starting point/origin
- To do so, press Tab on your keyboard to bring up the virtual MPG interface (if you do not have a hand wheel) and click on X Y axis button to manually control the motor work, to find the machining start point of the workpiece,as shown below:
- Zero the X, Y & Z coordinates as shown with the buttons below:
- Press CycleStart in order to start your program. You can also use Feed Hold to pause the program and of course Stop to stop the program permanently.
Notes on Mach3 Features
Reset Button
If 'Reset' is flashing ,the software will not work. If it cannot be reset, please check if the motion control is connected, Check software input settings.
Limit Switch Release
After the limit trigger, the software can't do anything. At this time, the ' Auto LimitsoverRide ' function can be used to restore the manual operation function. Once you have moved your CNC so the limit switch is no longer triggered, you can release limit trigger as shown in the figure:
Inverting Axis Directions
Returning CNC to Home
The limit switch can be used as the home coordinate switch, which can realize the automatic homing function. As shown in the figure below:
Mach Cnc Control
How did we do?
Mach3 Usb Software
Related Articles
(opens in a new tab)
Mach3 Software For Windows 10
1.Because of the interference, Mach3 cannot find the USB card
- Problem Description: control cards, when suddenly turn on the spindle, or for spindle speed adjustment.
- The problem: MACH3 software is stopping, status bar:
- please insert USB card.
- Solution: the problem is caused by interference
- Please connect the ground wire (PE) of the inverter and the ground wire of the shaft to the earth
- Connect the VFD PE Pin and spindle shell to the ground
2. In Constant velocity mode, In a straight line corner, walked out of mach3 is rounded.
- 2.1.1 In general setting, please choose constant velocity mode
- 2.1.2 In general setting, choose “stop cv on angle>6 degree”
- When drawing small circles, if the machine dithers, you can modify
- 6 degree into 12 degree. With this number become bigger, it moving
- faster when drawing. But straight line corner will be round.
- 2.1.3 It is not smooth when drawing little circle, you can see many line segments. at the same time, machine dithering.
- Now please modify the output code of drawing little circle into I, J Code. Then you can do it.
3. Mach3 back to origin point setting:
- 3.1nder Mach3 configure menu, open IO port/pin, then
- /input menu xhome,yhome ,zhome. set it Port# 1, Pin number :0,1,2 ,
- Active low: Ticked.
- 3.2 Open our driver: note mach3 /configure menu, open
- config plugins. Choose Ncpod. At homing menu please choose
- Single Stage/Dual stage.
- 3.3 Connect the origin switch wire; make sure switch signal is right.
- 3.4 Mach3 main interface choose ref home.
- 3.5 Executive command, start to back origin point
- If after back to origin point, direction and Switch is opposite, please
- Enter Mach3 configure, Open home/Limit, Tick the Home neg of the corresponding axis
4. How to adjust the spindle speed?
- 4.1 Connect the spindle control line like the picture showed.
- DCM, FWD belongs to Starting signal. Short circuit will start VFD. AVI, ACM are Analog voltage adjustment signal for spindle speed adjustment,10V is VFD output Voltage
- 4.2. Mach3 work, click spindle F5,move slider for speed adjustment.
- 4.3. Make sure that the speed not 0 now, if it is 0, Please input 10000 of spindle speed, and Enter. Check if the mach3 start signal is right
- 4.4. If the spindle is not started, please make sure that
- connection is right
- And VFD belong to analog voltage control
- 4.5 mach3 spindle start need to set 2 places
- 4.5.1 Set hardware port->Output port:
- Please make sure that Output #1- Output #8 are ticked, other not.
- 4.5.2 Spindle setting:
- 4.5.3 Tick Use spindle motor Output and PWM Control, and
- Clockwise Output set 1, CCW output set 2
- 4.5.4 Set Spindle Max Speed.
- Config menu ->Pulley selection Please set the Max Spindle speed into 24000
5. How to do tools setting?
- 5.1 Setting hardware port->input port, please tick Probe input signals.
- Pin Number should be corresponding with Inx of hardware card as follow output pin should be In4.
- 5.2Menu->Edit button scrip.t
- Click auto tool zero clearing
- 5.3 Copy the file m930.m1s in the CD we offered, save it and quit documents edit window.
- Then click auto tool zero clearing button, it starts to do auto tool guide.
- 5.4 For thickness of tool setting please set it in mach3 offset window.
6. How to manually move lathe and adjust moving speed
- 6.1 Press TAB key will show manual move window, enter
- Jog mode, you can switch it between Step and Continuous
- 6.2 Press X+, Y- then you can move the lathe
- 6.3 press+/- to adjust the moving speed percent, when it up to100%, moving speed will be Max.
- This is the motor speed of your motor adjustment
7. How to set software limit according to the size of lathe.
- 7.1 Back lathe origin, zero clearing Machine coordinate.
- Open Origin/Limit window in Config setting
- 7.3 Set soft ax as max positive, soft min as min negative, unit is mm/inch. This data can be set according to your size of machine. But This data is machine coordinate, not working coordinate
- 7.4. Press Software limit button, Open it. It will turn green
- If it is working normally
8. How to set limit switch?
- 8.1 if you use origin switch as limit switch, then you only need to open our driver plugin, tick LimitEn and corresponding origin, no need other setting.
- Generally speaking, A, B,C are rotation axis, no need limit.
- 8.2. If you got a special limit switch, and connect X++ and positive limit to the In8, you need to set it like below… Config – > hardware port: Input port please tick x++, set P1.8, and active low like the form below.
9. How to control feed speed when run G-code?
- Setting page, change feed adjustment into 3000, open rapid control button, now the speed of go will be F3000
10. How to calculate Steps per?
- Steps per is the number value that the machine move 1mm, unit is: pulse/mm
- Computational Formula: Screw drive:
- Steps per =
- (360 degree)/step angle*micro-stepping level/Screw lead
- Rack Gear: Steps per=
- (360 degree)/step angle*micro-stepping levels/
- transmission ratio/modulus*number of teeth*3.1415
- Unknown parameter
- if steps per is 200 pulse/mm, —-Input, enter
- manual processing mode then input g0x300 (it means when you input pulse X value the distance it will move
- 300mm) moving actual distance we call it a. Here is the
- Formula: X/300=200/a.
- right steps per X=200*(300/a)
11. How to set velocity and acceleration velocity correctly
- MACH3, Motor adjustment, please set velocity and like the form showed
- Generally, for stepper motor, value should be 100-500.
- For servo motor system, can be 400-1200
- Acceleration velocity should be set right,
- It maybe cause problems, like machine dither, lose step.
12. Mach3 Control Output IO-M code
- Activate Signal (OUTPUT5) Open Output port5
- Deactivate Signal (OUTPUT5) Close Output 5
- Please copy m200, m201 to c: mach3/macro/mach3mill
- In programming, input m200 open output 5, M201 close output 5
- User can change OUTPUT5 into OUTPUT6, And then you can control other
- Output Port.
- In Mach3 diagnosis, If Output 5 is flashing, it shows that Output port opened